Bag Filters, Silos & Dust Collection Systems
Particulate Control and Powder Storage Solutions for Clean Operations
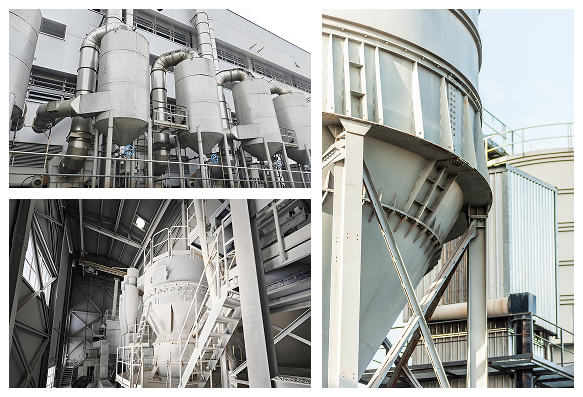
Shree Shakti Engineering Works manufactures a wide range of bag filters, silos, and dust collection systems to control air pollution, improve workplace safety, and support powder handling and storage in chemical, pharmaceutical, cement, agrochemical, and food industries.
Our solutions are tailored to meet dry particulate separation, bulk storage, and material transfer needs with robust construction, low maintenance, and high reliability — ensuring compliance with environmental and process standards.
Systems Offered
Bag Filters & Dust Collection Units
- Pulse Jet Bag Filter
- Manual Shaking / Reverse Air Bag Filter
- Cartridge Filter Systems
- Vent Filters for Silos & Reactors
- Hopper Bottom Collection with Rotary Valves or Screw Conveyors
Accessories / Systems
- Ducting, Dampers, Isolation Valves
- RAV (Rotary Airlock Valves), Diverter Valves
- Screw Conveyors for Powder Transfer
- Explosion Vent / Rupture Discs (for dusty zones)
Design Inputs Required (From Client)
Parameter | Required Details |
---|---|
Air Flow Rate (Bag Filter) | m³/hr or CFM |
Dust Load / Particle Type | Powder name, concentration, particle size |
Powder Storage Capacity (Silo) | KL or Ton requirement |
MOC | SS304, SS316, IS 2062, FRP, HDPE, etc |
Mounting | Skid, Structure, RCC base |
Cleaning Type (Bag Filter) | Pulse Jet / Manual / Reverse Air |
Automation | Basic, Semi-Auto, or Fully PLC Controlled |
Safety Requirements | Zone classification, flameproof rating (if any) |
Design Specifications
Airflow Range | 500 m³/hr to 30,000+ m³/hr |
Silo Volume | 2 KL to 100 KL (Custom on-site fabrication possible) |
Bag Material | Non-woven Polyester, PTFE, Nomex, Antistatic |
Filtration Efficiency | Up to 99.9% for particles ≥1 micron |
MOC Options | SS304 / SS316 , MS / IS 2062 + Paint / Epoxy / Powder Coating , FRP or Plastic-lined (on request) |
Finish | Painted, Pickled, Passivated, or Epoxy Coated |
Design Codes & Standards
- IS 11213 / IS 9188 – For dust collection units
- SMACNA / ASHRAE Guidelines – For duct design
- CPCB / GPCB Emission Norms – Compliant design
- ASME Section VIII (where pressurized)
- EN / ATEX – For explosive environments
Quality Control & Inspection
- Raw Material & Welding Inspection
- Agitator Alignment & Load Testing
- Hydro & Pneumatic Pressure Testing
- Surface Roughness Inspection (for GMP)
- Radiography / DPT / UT as per weld class
- Final Validation & TPI Witness (as applicable)
Quality Control & Inspection
- Bag Filter Flow & Leak Test
- Silo Hydrotest / Weld Inspection
- Paint Thickness & Surface Prep Testing
- Blower Alignment & Trial Run
- Documentation – MTCs, Drawings, Test Reports
- Third Party Inspections
Optional Features / Customizations
- Hopper Heater / Fluidizing Pads
- Rotary Valve, Screw Conveyor, Vibratory Discharge
- Control Panel with Timer / PLC / DP-based Auto Cleaning
- Flameproof Electricals for Hazardous Zones
- Pressure Gauge, Level Sensors, Sight Glasses
- Safety Ladders, Platforms, Railings
Industries Served
- Agrochemical & Fertilizer Plants
- Cement, Minerals & Construction Material
- API & Pharmaceutical Powder Handling
- Dyes, Pigments & Fine Chemicals
- Food, Spices, and Starch Units
- Pesticides / Intermediates
- Boiler Ash Collection & Utility Dust Control