Heat Exchangers
- Home
- Heat Exchangers
Shell & Tube Heat Exchangers
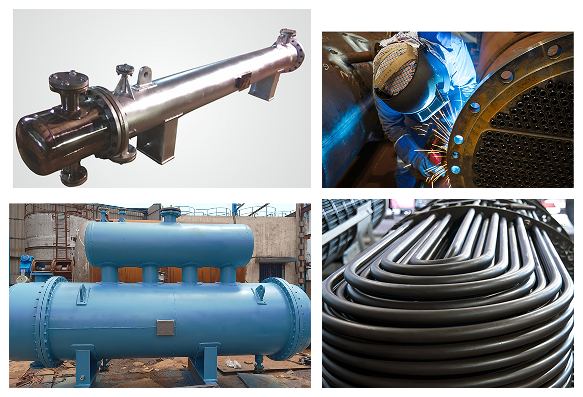
At Shree Shakti Engineering Works, we design and manufacture high-efficiency Shell & Tube Heat Exchangers to handle challenging thermal duties across chemical, petrochemical, pharmaceutical, and allied industries. Our exchangers are optimized for both thermal performance and mechanical strength, and built in accordance with TEMA, ASME, and IS standards.
We offer solutions using plain, corrugated, or finned tubes, depending on process needs such as heat transfer rate, pressure drop, and fouling behavior.
Functional Classification
Our heat exchange equipment is designed for various functional roles in process systems :
- Heat Exchanger – General-purpose thermal energy transfer between fluids
- Condenser – Vapor to liquid phase change via cooling
- Reboiler – Liquid vaporization for distillation columns
- Evaporator – Concentration of solutions via solvent evaporation
- Cooler / Chiller – Temperature reduction of process streams
- Heater / Preheater – Raising fluid temperature before reaction or mixing
Construction Types Offered
- Fixed Tube Sheet – For clean, non-corrosive fluids
- U-Tube Bundle – For thermal expansion tolerance
- Floating Head – Easy cleaning and maintenance access
- Double Pipe / Hairpin Type
- Multi-Pass Tube Side Design – 1-1, 1-2, 2-4 passes for efficient performance
Basic Design Inputs Required (From Client)
Parameter | Required Details |
---|---|
Fluids (Shell / Tube Side) | Type, phase, corrosion/fouling tendency |
Flow Rates | In LPH / m³/hr |
Inlet & Outlet Temperatures | Required at (temperature difference) |
Design Pressure & Temperature | Shell and Tube sides separately |
MOC (Material of Construction) | SS304, SS316L, SA516, Duplex, etc |
Tube Side / Shell Side Preference | Based on media compatibility |
Mounting Orientation | Horizontal / Vertical |
Design Specifications
- Heat Transfer Area – 0.5 m² to 300 m²
- Design Pressure – Vacuum to 40 bar (higher on request)
- Design Temp Range – Up to 400°C
- Tube Dia Options – 12.7 mm, 15.88 mm, 19.05 mm, etc.
- MOC – SS304, SS316, SS316L, SA516, Duplex, Hastelloy
Tube Types
- Plain Tubes
- Corrugated Tubes – For turbulence & enhanced transfer
- Finned Tubes – For air/gas-side efficiency improvement
Design Codes & Standards
Our Shell & Tube Heat Exchangers are designed as per international thermal and mechanical design codes to ensure optimal performance, safety, and regulatory compliance across industries and geographies.
- TEMA (B, C, R Class) – Mechanical configuration, thermal design, and exchanger layout
- ASME Section VIII, Div. 1 – Pressure boundary compliance for shell and tube sides
- IS 4503 / IS 2825 – Indian standards for fabrication and design of pressure-bearing components
- API 660 – Design of heat exchangers in oil & gas and refinery systems
- EN 13445 / PED 2014/68/EU – European Pressure Equipment Directive
- Client-Specific Standards – EPCs, MNCs, consultants, or international spec sheets
Quality Control & Inspection
All exchangers are subjected to multi-stage inspections and stringent testing to ensure mechanical integrity and thermal performance. We follow documented QA/QC procedures aligned with customer and TPI requirements.
- WPS/PQR Qualified Welders & Procedures
- Bundle Testing / Air Leak Testing (optional)
- Third-Party Inspections by leading agencies
Inspection Stages
- Raw Material Inspection (MTC validation)
- In-process Weld & Fit-up Checks
- Dimensional Inspection
- Final Visual Inspection
Non-Destructive Testing (NDT):
- Radiography Testing (RT)
- Ultrasonic Testing (UT)
- Dye Penetrant Testing (DPT)
- Hydrostatic & Pneumatic Pressure Testing
- Eddy Current testing of Tubes
Optional Features / Customizations | Industries Served |
---|---|
Expansion Bellows | Agrochemicals & Fine Chemicals |
Removable or Fixed Tube Bundles | Pharmaceuticals & Intermediates |
Segmental / Rod / Double Baffles | Petrochemicals & Refineries |
Grooved or Seal-Welded Tube Sheets | Dyes & Pigments |
Pass Partition Plates (2, 4, 6 pass) | Food, Dairy & Beverage |
Thermowells, Vents, Drains, Nozzles | Utilities / Power Plants / HVAC |
Mounting Saddles, Skid Frames, Lifting Lugs | Waste Heat Recovery Units |
Painting / Passivation / Pharma-Grade Finish |