Pressure Vessels / Receivers
Engineered for Safe Containment of Pressurized Fluids
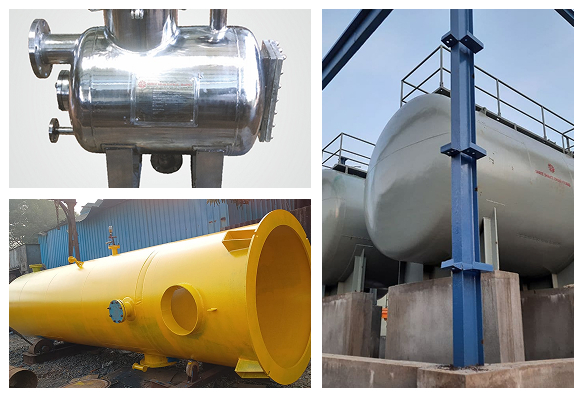
At Shree Shakti Engineering Works, we specialize in the design, fabrication, and testing of pressure vessels and receivers for safe storage and handling of gases, vapors, and pressurized liquids. Each vessel is custom-designed to meet project-specific pressures, temperatures, and process media in compliance with ASME, IS, and IBR standards.
Our vessels are used across chemical, petrochemical, pharmaceutical, utility, and gas processing industries, and are built for long service life, mechanical integrity, and third-party verified safety.
Types of Pressure Vessels & Receivers
- Vertical & Horizontal Vessels
- Surge Tanks / Air Receivers / Buffer Vessels
- Vacuum Receivers / Degassers
- Knockout Drums / Separator Vessels
- Coil / Jacketed Vessels for Heating or Cooling
- Cladded or Dual-Material Vessels
- Receiver Tanks for Compressors / Utilities
- IBR Certified Steam Drums / Blowdown Vessels
Design Inputs Required (From Client)
Parameter | Required Details |
---|---|
Design Pressure & Temperature | Internal and/or external conditions |
Working Volume / Capacity | Litres / KL / M³ |
Fluid Details | Gas, vapor, liquid, or multiphase service |
MOC (Material of Construction) | SS304, SS316L, SA516 Gr.70, Duplex, etc |
Mounting Orientation | Horizontal / Vertical |
Nozzles & Accessories | Inlets, outlets, manholes, vents, drains |
Internal Coils / Jackets (if any) | With medium specifications |
Painting / Coating Requirements | Internal / External |
Design Specifications
Volume | 50 Litres to 100 KL |
Pressure Range | Vacuum to 40 bar (customizable) |
Temperature Range | -20°C to +400°C |
MOC | SS304, SS316L, SA516 Gr.70, Duplex, Cladded |
Surface Finish | Painted, Grit Blasted, Pickled & Passivated |
Mounting | Skirt, Leg, Saddle, Platform-supported |
Types of Pressure Vessels & Receivers
Our pressure vessels are designed and manufactured in strict compliance with globally recognized engineering standards, ensuring performance, durability, and safety under varying operating conditions.
- ASME Section VIII, Div. 1 – Design & fabrication of pressure vessels (International)
- IS 2825 – Indian standard for unfired pressure vessels
- IBR (Indian Boiler Regulations) – For steam vessels and boiler accessories
- API 620 / API 650 – For large storage or low-pressure applications (if applicable)
- PED / EN 13445 – European Pressure Equipment Directive
- Client-Specific Specifications – For EPC, OEM, and international projects
Quality Control & Inspection
Each vessel undergoes rigorous QA/QC procedures throughout the manufacturing cycle, supported by qualified personnel and documented traceability.
- WPS / PQR Qualified Welders as per ASME / IBR / EN codes
- Hydrostatic / Pneumatic Testing
- Stage-wise & Final Visual Inspection
- Material Test Certificates (MTCs) & Internal Test Reports
- Third-Party Inspection (TPI) from agencies
NDT Methods
- Radiography Testing (RT)
- Dye Penetrant Testing (DPT)
- Ultrasonic Testing (UT)
- Magnetic Particle Testing (MPT)
Optional Features / Customizations | Industries Served |
---|---|
Internal Coils (SS / CS) for heating/cooling | Pharmaceuticals & Intermediates |
Spray Nozzles, Dip Pipes, Thermowells | Agrochemicals & Fertilizers |
Rupture Discs, Safety Valves, Flame Arrestors | Oil & Gas |
Insulation & Cladding (SS / Aluminum)/td> | Food & Beverage |
Load Cell Mounting for Weighing | Utilities – Steam, Compressed Air, Vacuum |
Access Platforms, Ladders, Lifting Lugs | Power Plants & Boiler Houses |
Earthing Lugs, Nameplates, and Base Frames | Paints, Dyes & Pigments |
Skid-Mounted Systems for transportable use |