Reactors
Custom-Engineered Process Reactors with Heating, Cooling & Agitation
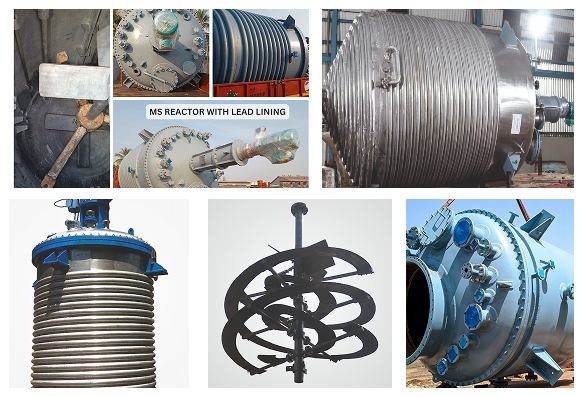
Shree Shakti Engineering Works designs and fabricates high-performance chemical process reactors used in batch operations across pharma, agrochemical, specialty chemical, and allied industries. Built to handle heating, cooling, agitation, and pressure variations — our reactors are tailored to meet demanding process and material requirements.
Types of Reactors (by Utility & Design)
- Jacketed Reactors – External jacket for controlled thermal circulation
- Limpet Coil Reactors – Half-pipe coil for efficient indirect heating/cooling
- Internal Coil Reactors – Immersed coils for direct medium contact
- Combined Jacket + Limpet Design – For staged or dual utility systems
- Vacuum / Pressure Reactors – Designed for sealed batch operations
- Pilot & Modular Skid Reactors – Compact, lab-scale, or mobile units
Agitator Types
We offer a wide range of agitators tailored to your process needs, including anchor, turbine, propeller, ribbon, and helical designs. Impeller selection is based on viscosity, mixing objectives, and process parameters to ensure efficient and uniform performance.
Radial Flow Impellers
Best for low-to-medium viscosity fluids and gas dispersion. Flow is directed outward from the impeller.
- Turbine Impeller (Straight Blade or Flat Blade) – General-purpose mixing, gas dispersion
- Rushton Turbine – Ideal for gas-liquid dispersion (fermentation, aeration)
- Disc Turbine – Balanced shearing and flow, for emulsion-type mixing
- Pitched Blade Turbine (45°) – Versatile, suitable for both axial and radial flow
Axial Flow Impellers
Direct flow downward or upward, ideal for heat transfer, blending, and solids suspension.
- Propeller Impeller (3-Blade / Marine Type) – High-speed axial flow, low viscosity mixing
- Pitched Blade Impeller (60°) – More axial thrust than standard turbines
- Hydrofoil Impeller (High Efficiency) – Energy-efficient for high-volume, low-viscosity systems
Tangential / Mixed Flow Impellers
Create a swirling flow, often for heat-sensitive or shear-sensitive products.
- Anchor Type – For viscous fluids, effective near wall scraping
- Gate Impeller – Similar to anchor, used for large flat-bottomed vessels
- Helical Ribbon Impeller – Ideal for high-viscosity materials like gels and creams
- Screw Impeller / Helix Coil – Used in vertical vessels, promotes upward or downward axial flow
- Cage Impeller / Frame Agitator – Combines axial and tangential flow in large reactors
Specialized / High-Shear Impellers
- Vortex-type Impellers – Custom designs to create strong vortex motion
- Sawtooth High-Shear Disperser – For emulsification, dispersion of solids in liquids
Impeller Selection Depends On :
- Viscosity of Medium
- Solid Content (if any)
- Tank Geometry
- Heat Transfer Requirement
- Shear Sensitivity
- Mixing Time & Power Constraints
Gearbox Options
- Inline Helical
- Planetary Gearbox
- Worm Gearbox
- Helical Bevel
- Bevel Gear
- Custom Drive Assemblies
Motor Options
- Standard Foot/Flange Mount Motors
- Flameproof (FLP) / Non-FLP Motors
- Energy-Efficient IE2/IE3/IE4 Motors
- VFD-Compatible Motors (with or without panel)
Bearing Options
- Self-aligning Ball Bearings
- Deep Groove Ball Bearings
- Taper Roller Bearings
- Pillow Block / Flange Mount Bearings
Sealing Systems
- Gland Box Sealing
- Double Mechanical Seal (Back-to-Back or Tandem)
- Cartridge Seal Assemblies
- Magnetic Drive Sealing (optional)
Design Inputs Required (from Client)
Parameter | Required Details |
---|---|
Capacity | Working & Total Volume (Litres/KL) |
Operating Pressure | Vacuum to 10 bar (or as specified) |
Operating Temperature | Heating / Cooling range |
Material of Construction (MOC) | SS304, SS316L, SA516 Gr.70, Duplex, etc |
Utility Mediums | Steam, Thermic Fluid, Brine, Chilled Water |
Agitation Specs | Type, RPM, Torque, Viscosity Consideration |
Mounting Type | Leg / Skirt / Lugs / Platform Supported |
Accessories | Nozzles, Manholes, Instrumentation, etc |
Design Specifications
Volume | 100 Litres to 50 KL |
Pressure | Full vacuum to 20 bar or more |
MOC | SS304 / SS316 / SS316L / SA516 Gr.70 / Duplex / Hastelloy |
Surface Finish | Mirror, Grit, Pickled & Passivated |
Pharma Finish | Electropolished / Mirror Finish (0.4–0.6 Ra) – GMP / cGMP compliant |
Insulation | Mineral/Glass wool with SS or Aluminum Cladding |
Design Codes & Standards
- ASME Section VIII, Div. 1 – Pressure Vessel Design
- IS 2825 – Indian Standard for Pressure Vessels
- WPS/PQR Certified Welding as per Code
- TPI Inspection
Optional Features & Add-ons | Industries Served |
---|---|
Internal Coils (SS or CS) | Pharmaceuticals & cGMP Manufacturing |
Spargers, Dip Pipes, Thermowells | Agrochemicals & Pesticides |
Baffles, Reflux Condensers | Specialty Chemicals & Intermediates |
Load Cell Mounting | Dyes & Pigments |
VFD Panels, Temperature Controllers | Oilfield & Petrochemicals |
Skid Base, Platforms, Ladders, Railings | Pilot Plants & R&D Labs |
Insulation & Cladding Options | Food & Biotech Processing |
CIP/SIP Nozzles for GMP applications |